Paper in its most advanced form.
Our product range of Unicolour, Print Base Papers, Backer Papers and Underlay.
A collection dedicated entirely to the requirements of the furniture industry.
The production process Full screen
Water is the original source.
Water, originating entirely from a shut-off water supply from the river Cosa is our most important resource: it makes up 95% of our raw materials.
water
cellulose
titanium dioxide
pigments
95%
3,5%
1,25%
0.25 %
The cellulose fibers used in our production are FSC certified and are obtained from Sotuh American and Iberian eucalyptus and northern conifers. The pigments are made up of iron oxide.
The core of production
The continuous cycle machine makes up the central phrase in which the actual conversion of the product takes place. This conversion is developed through a series of consecutive phases that convert the initial liquid pulp into real paper.
- Drainage
- Press
- Pre Drying
- Post Drying
- Calendering
- Winding and Reeling
- The pulp is distributed through the headbox on the flat table. Here the separation of the water part (99%) and the fibrous part of the pulp takes place.
- The separation phase continues in the press. At the end of which the fiber content as compared to the water content is approximately 50%.
- In this phase the water content in the paper sheet decreases to 25% allowing for a controlled drying span for every type of product.
- In this phase the water content in the paper sheet falls to 3%. At the end of this drying process the paper sheet reaches the required level of humidity in order to ensure an outstanding product without any residual stiffness.
- The sheet is crushed between 2 rollers, the first one is soft and the secondi s a high surface finish one. At the end of this process the paper sheet has all the surface qualities required in order to guarantee an outstanding level of printability.
- The paper is wrapped around poles with a maximum weight of approximately 500-600 kilograms and a maximum size of 280 cm. The paper is then handled by the Winding Machine, where the reels are prepared according to the Clientís request.
Quality is our main objective.
We are able to develop a flawless sheet thanks to a precise phototyping phase and subsequent visual monitoring during the continuous cycle process.
An in-depth post production control process.
We detect and monitor for flaws so as to ensure the productís high performance in the printing and impregnation phase.
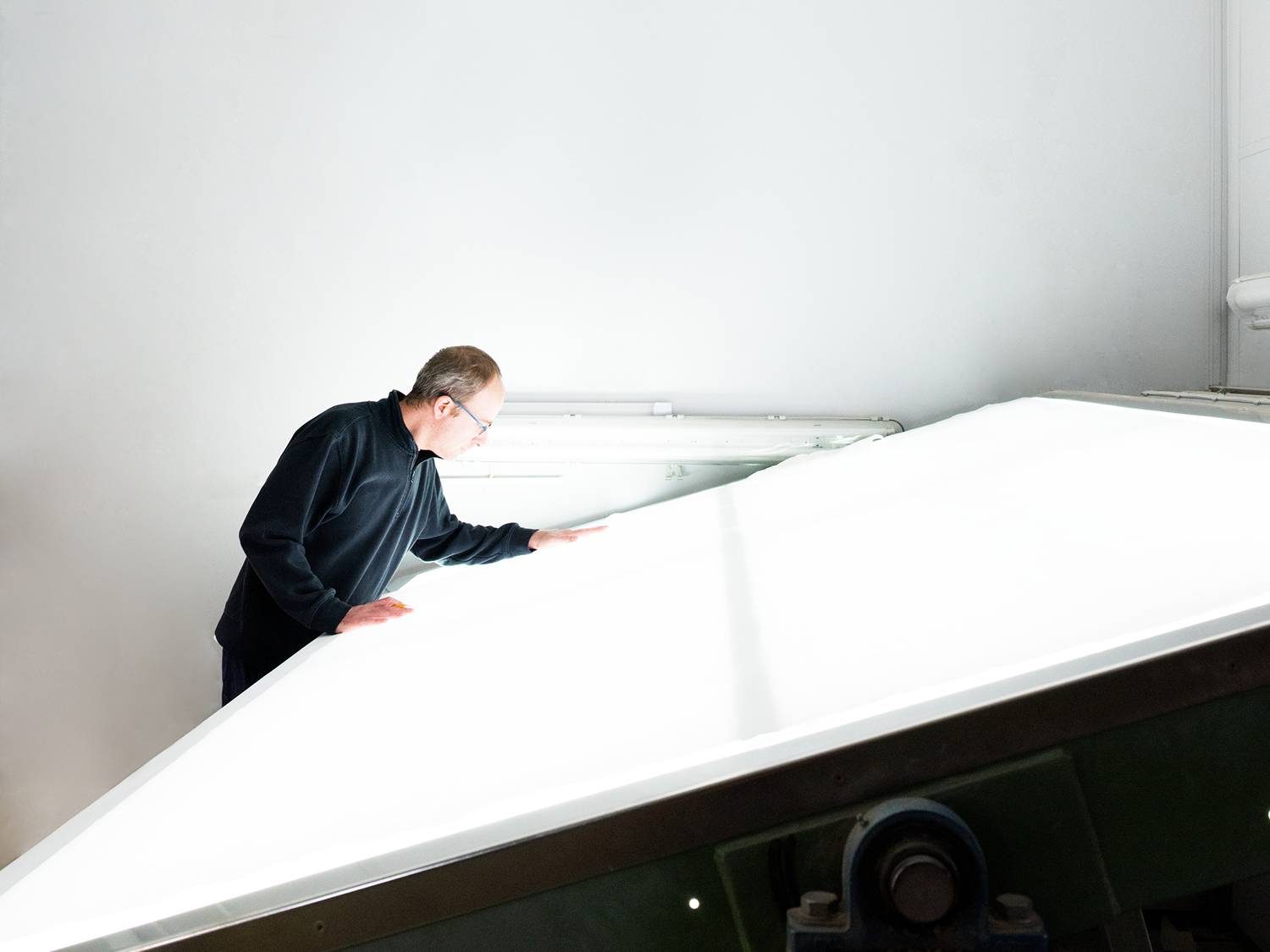
A qualified technician at work, meticulously monitoring the finished product.
Cartiere di Guarcino
Privacy – Cookies Policy | Legal Notices
Neodecortech
Whistleblowing
copyright @ 2018